PFA Film
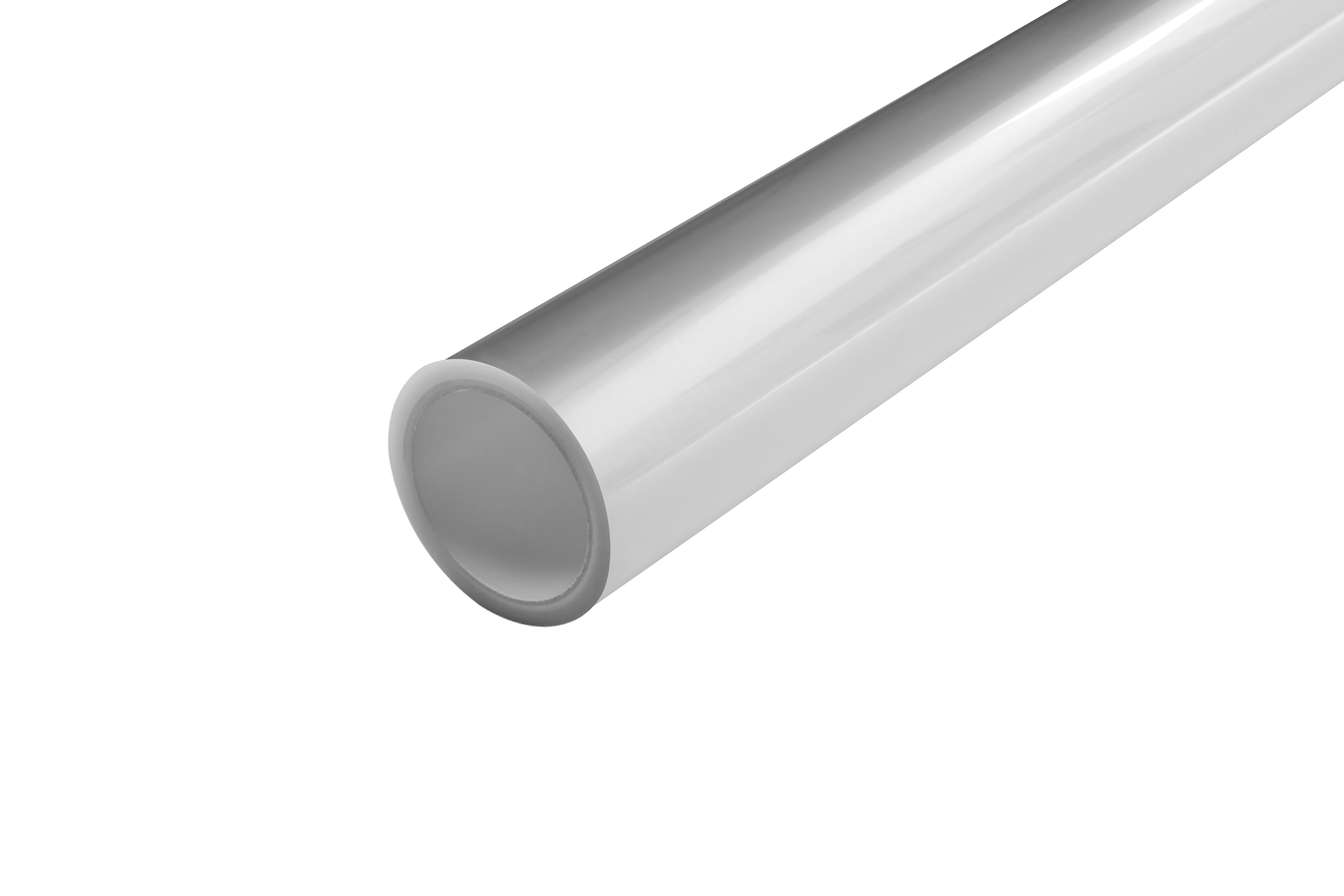
PFA Film/PFA Foil
ESONE PFA film is manufactured using a melt extrusion casting process from Perfluoroalkoxy (PFA) polymer resin. This film boasts the highest continuous use temperature of any melt-processable fluoropolymer film, reaching 260°C (500°F). The PFA film provides many of the performance characteristics of PTFE in a clear and transparent format, and it can be heat sealed, thermoformed, welded, metallized, or laminated to various materials.
Advantages of PFA Film
ESONE’s PFA films provide all the benefits of fluorinated films, including:
- Wide Temperature Resistance: Continuous service temperature range from -425 to 500°F (-254 to 260°C), making them suitable for extreme environments.
- High Melt Temperature: Melt temperature range of 572 to 590°F (300 to 310°C) allows for versatile processing options.
- Chemical Inertness: Resistant to virtually all chemicals, ensuring durability and longevity in aggressive environments.
- Outstanding Dielectric Properties: Excellent dielectric performance over a wide range of frequencies and temperatures, ideal for electrical applications.
- High Dielectric Strength: Provides over 6,500 V/mil (260 kV/mm for 25 micron film), ensuring effective insulation and safety in high-voltage applications.
- Optical Clarity: Excellent light transmission and clarity, making them suitable for applications requiring transparency.
- Additive-Free Composition: Free of plasticizers, processing aids, or additives, ensuring a pure material with consistent properties.
These advantages make melt process fluoropolymers ideal for a variety of demanding applications in industries such as aerospace, electronics, and chemical processing.
ESONE PFA films are available in two grades
- Made from 100% virgin premium grade PFA resin with a melt flow index (MFI) range of 1.5 to 2.5.
- PFA GP is the preferred choice for dielectric applications and situations where exceptional visual clarity and perfection are essential.
- Provides significant cost savings of 30% compared to GP grade while retaining all the physical, mechanical, and thermal properties of General Purpose PFA film
- An ideal economical solution for heat sealing, welding, and other melt adhesive applications where high aesthetic standards are not required.
Specification of PFA Film
ESONE offers PFA films with thickness ranging from 0.012 to 0.25mm (12 to 250 um) (0.0005 inches to 0.010 inches), with a standard width of up to 1,600 mm (63 inches). Additionally, slit widths and bondable surfaces (plasma treated or chemically etched) are available upon request.
Width: Max 1,600mm (63 inches) Any slit width is available
Surface: Non-treatment, plasma treated or chemically etched
Temperature: Continuously working in temperatures ranging from -254°C to 260°C (-425 to 500°F )
Applications of PFA film
PFA foils are widely used across various industries, particularly in environments that require high temperature and chemical resistance. They are suitable for:
- Circuit Board Fabrication: Ideal for reliable performance in electronic applications due to its chemical and thermal resistance.
- Flat Cable Insulation: Provides robust electrical insulation for flat cables in modern devices.
- Electrical Insulation: High-temperature stability makes it suitable for various insulation needs.
- High-Temperature Release Film: Functions effectively in composite manufacturing processes.
- Vacuum Bagging Film: Used in composite applications, withstanding curing temperatures up to 230°C (446°F).
General Properties | Test Method | PFA GP – General Purpose | PFA WF – Welding Film |
---|---|---|---|
Specific Gravity | 2.15 | ||
Area Yield m²/kg/mm (ft²/lb/mil) | 727.4(90) | ||
Flammability | UL-94 | V-0 | |
Water Absoption % | <0.01 | ||
Standard width mm(in) | Max 1,600mm (63 inches) Any slit width is available | ||
Thickness Available mm(mil) | 0.012 to 0.25mm (0.5 to 10 mil) | ||
Color | Clear | ||
Mechanical Properties | |||
Tensile Strength MPa(psi) | ASTM D882 | 35(5,000) | |
Elongation at Break % | ASTM D882 | 500 | |
Tensile Modulus MPa(psi) | ASTM D882 | 483(70,000) | |
Initial Tear Strength g/mm(g/mil) | ASTM D1004 | 9,840(250) | |
Propagation Tear Strength g/mm(g/mil) | ASTM D1922 | 1,470(37.5) | |
Folding Endurance (MIT) cycles | ASTM D2176 | 100,000 | |
Thermal Properties | |||
Continuous Use Temp ℃(℉) | UL-746B | 260(500) | |
Melt Point ℃(℉) | ASTM D3418 | 302-310(575-590) | |
Electrical Properties | |||
Dielectric Strength volts/mm(volts/mil) | ASTM D149 | 256,000(6,500) | N/A |
Dielectric Contant 1kHz | ASTM D150 | 2.0 | N/A |
Dissipation Factor 1kHz | ASTM D150 | 0.0002 – 0.0007 | N/A |
Optical Properties | |||
Refractive Index | ASTM D542 | 1.35 | N/A |
Solar Transmission % | ASTM E424 | 96 | N/A |
Surface Treatments Available | |||
Chemical Etching | Available | ||
Plasma Treatment | Available | ||
Applications | |||
Composite Molding Process: Release Films | |||
Chemical Process/Equipment | √ | √ | |
Heat Sealing/Welding/Melt Adhesive | √ | ||
Electrical/Electronics | √ | ||
Medical | √ | ||
Optical /Photovoltaics | √ | ||
Protective/Decorative | √ |