FEP Film

FEP Film/FEP Foil
ESONE FEP film is manufactured using a melt extrusion casting process from Fluorinated Ethylene Propylene (FEP) resin. These films provide all the advantages of fluorinated materials, including exceptional temperature and chemical resistance, non-stick characteristics, and excellent dielectric performance. FEP films can be heat-sealed, thermoformed, laminated to different substrates, and utilized as melt adhesives.
Advantages of FEP Film
ESONE’s FEP films provide all the benefits of fluorinated films, including:
- High Temperature and Chemical Resistance: FEP films remain stable even in harsh environments.
- Non-Stick Properties: With superior anti-stick and low friction characteristics, they perform exceptionally well in various applications.
- Excellent Dielectric Performance: Ideal for electronic and electrical applications.
- Heat-Sealing and Thermoforming Capabilities: Can be laminated to various substrates and serve as melt adhesives.
- Outstanding Light Transmission and Clarity: Ensures product quality while maintaining transparency.
ESONE FEP films are free from plasticizers, processing aids, or additives, making them safe for food contact
ESONE FEP films are available in four grades
- Made from 100% virgin premium-grade FEP resin with an MFI range of 5-10.
- Ideal for applications that demand high dielectric performance, such as PCB laminates and wire & cable uses.
- Preferred for protective, decorative, and transparent applications where visual clarity is crucial.
- Complies with ASTM D3368 specifications for Type I FEP film.
- Provides significant cost savings of 30% compared to GP grade.
- An ideal economical solution for heat sealing, welding, and other melt adhesive applications where high aesthetic standards are not required.
- Complies with ASTM D3368 standards for Type I general-purpose FEP film.
- Available in various perforated patterns.
- It offers high elongation and excellent conformability to complex contoured molds.
- Standard colors include red, violet, and clear, with custom colors available upon request.
- With its exceptional non-stick properties and service temperature of up to 400°F (205°C), FEP is the preferred material for high-temperature composite molding.
- Complies with ASTM D3368 standards for Type IV mold release FEP film.
- Ideal for chemical tank linings, pump diaphragms, and rupture discs.
- Provides excellent stress-crack resistance and flex endurance, achieving 250,000 cycles in the MIT test.
- Complies with ASTM D3368 standards for Type III FEP film.
Specification of FEP Film
ESONE offers FEP films with thicknesses ranging from 0.012 to 0.25mm (12 to 250 um) (0.0005 inches to 0.010 inches), with standard widths up to 1,600 mm (63 inches). Additionally, slit widths and bondable surfaces (plasma treated or chemically etched) are available upon request.
- Width: Max 1,600mm (63 inches)
- Color: Transparent, Red, Blue and others
- Surface: Non-treatment, plasma treated or chemically etched
- Temperature: Continuously working in temperatures ranging -240°C to 205°C (-400°F to 400°F )
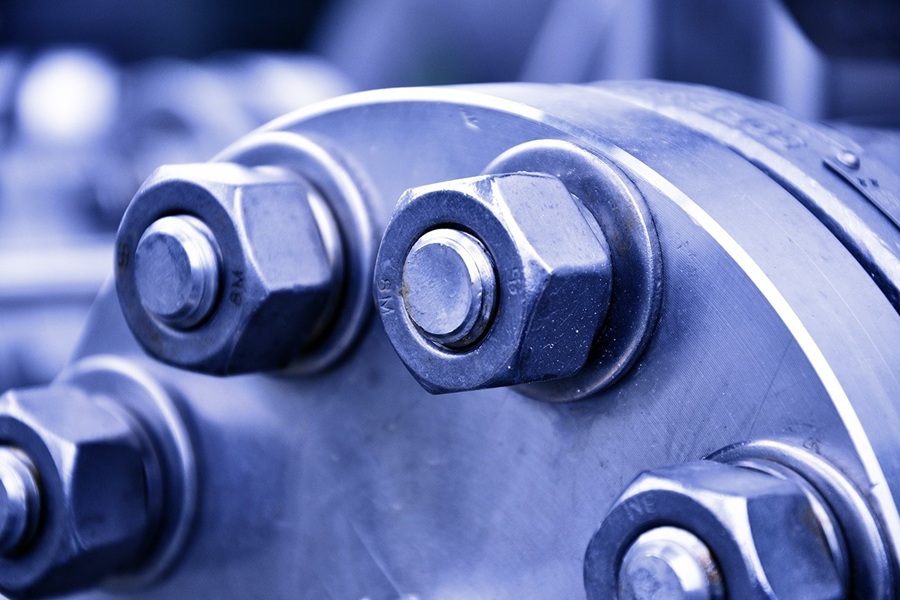
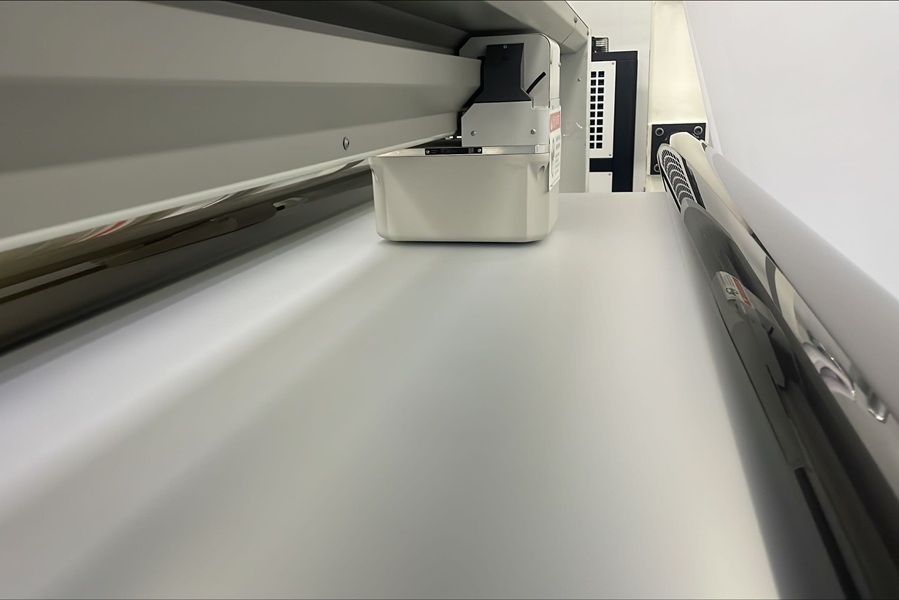
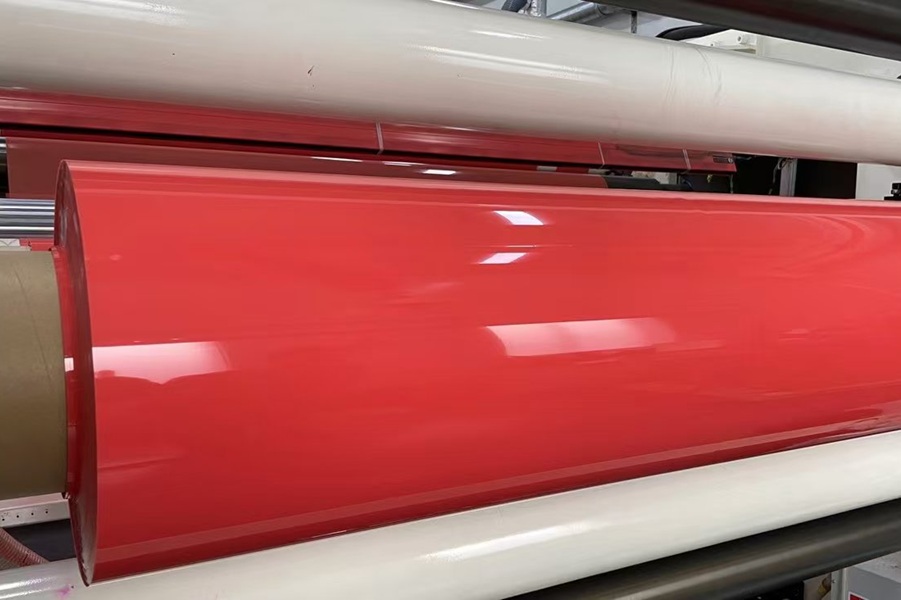
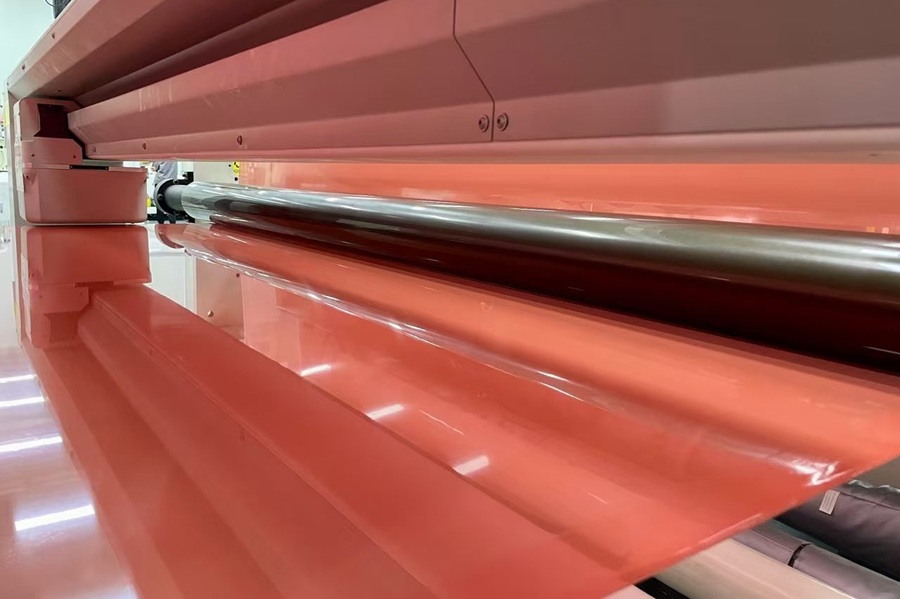
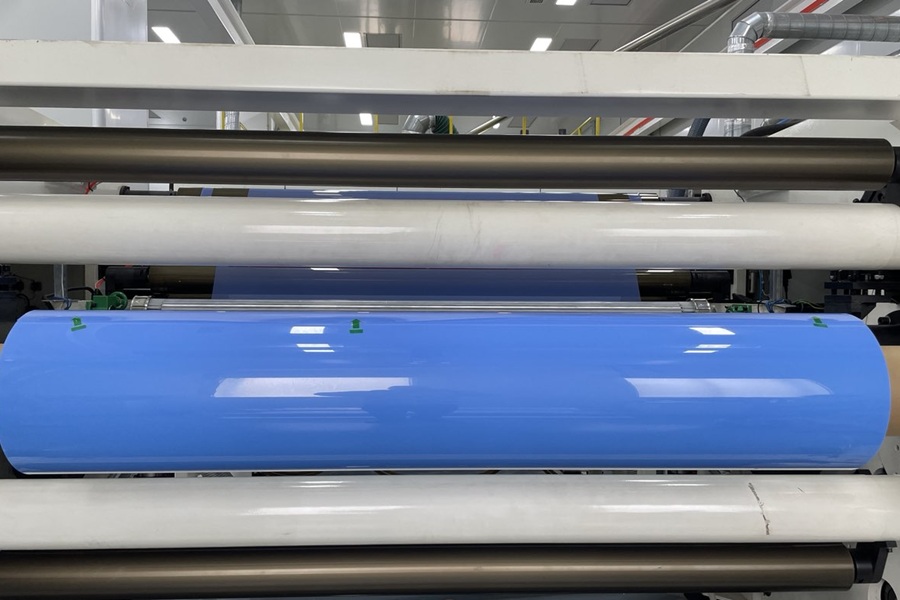
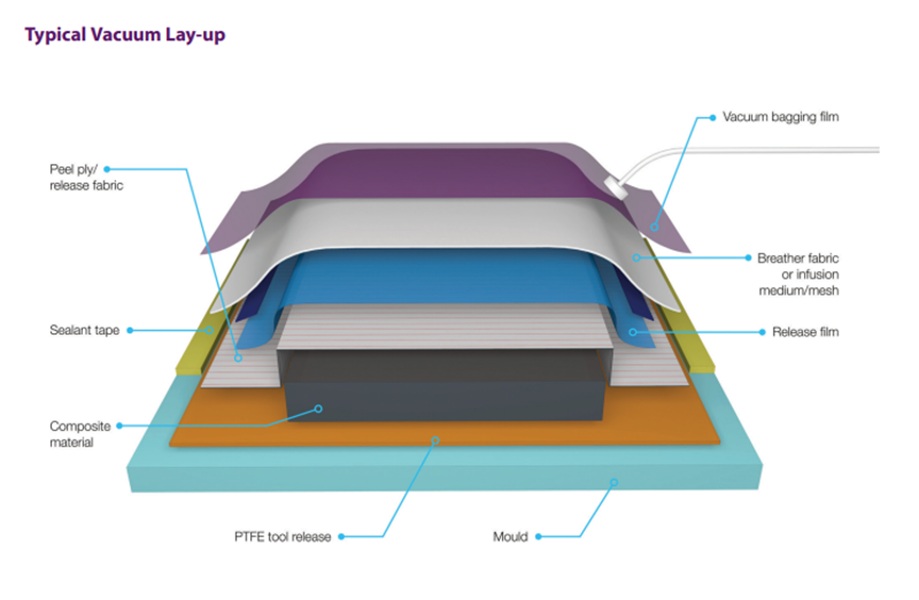
Applications
FEP films are widely used across various industries, particularly in environments that require high temperature and chemical resistance. They are suitable for:
- High Temperature Composite Molding: Preferred material for mold release applications due to maximum service temperature of 400°F (205°C).
- Complex Contoured Molds: Features high elongation and excellent conformability.
- Electronics: Their excellent dielectric performance makes them suitable for PCB laminates, electrical insulation and cable protection.
- Protective and Decorative Uses: Suitable for applications where visual appearance and clarity are essential, such as decorative films and see-through applications.
- Medical Devices: Compliant with USP VI standards, they are suitable for manufacturing medical instruments and devices.
- Industrial Applications: Used in chemical, pharmaceutical, and other industries as a durable material resistant to corrosion and high temperatures, like chemical tank lining.
Test Method | FEP GP – General Purpose | FEP WF – Welding Film | FEP MR – Mold Release | FEP HM – High Molecular Weight | |
---|---|---|---|---|---|
General Properties | |||||
Specific Gravity | ASTM D792 | 2.15 | |||
Area Yield m²/kg/mm (ft²/lb/mil) | 727.4(90) | ||||
Flammability | UL-94 | V-0 | |||
Water Absoption % | <0.01 | ||||
Standard width mm(in) | Max 1,600mm (63 inches) Any slit width is available | ||||
Thickness Available mm(mil) | 0.012 to 0.25mm (0.5 to 10 mil) | ||||
Colors | Clear | Clear | Red, Blue, Violet | Clear | |
Mechanical Properties | |||||
Tensile Strength MPa(psi) | ASTM D882 | 24(3,500) | 34.5(5,000) | ||
Elongation at Break % | ASTM D882 | 300 | 350 | ||
Tensile Modulus MPa(psi) | ASTM D882 | 483(70,000) | |||
Initial Tear Strength g/mm(g/mil) | ASTM D1004 | 10,830(275) | |||
Propagation Tear Strength g/mm(g/mil) | ASTM D1922 | 4,922(125) | |||
Folding Endurance (MIT) cycles | ASTM D2176 | 10,000 | 250,000 | ||
Thermal Properties | |||||
Continuous Use Temp ℃(℉) | UL-746B | 400(205) | |||
Melt Point ℃(℉) | ASTM D3418 | 500(260) | 520(270) | ||
Electrical Properties | |||||
Dielectric Strength volts/mm(volts/mil) | ASTM D149 | 256,000(6,500) | N/A | 256,000(6,500) | |
Dielectric Contant 1kHz | ASTM D150 | 2.0 | N/A | 2.0 | |
Dissipation Factor 1kHz | ASTM D150 | 0.0003 | N/A | 0.0003 | |
Surface Resistivity ohm/sq | ASTM D257 | 1x10^15 | N/A | 1x10^15 | |
Optical Properties | |||||
Refractive Index | ASTM D542 | 1.34 | N/A | 1.34 | |
Solar Transmission % | ASTM E424 | 96 | N/A | 96 | |
Surface Treatments Available | |||||
Chemical Etching | Available | ||||
Plasma Treatment | Available | ||||
Applications | |||||
Composite Molding Process: Release Films | √ | ||||
Chemical Process/Equipment | √ | √ | √ | ||
Heat Sealing/Welding/Melt Adhesive | √ | √ | |||
Electrical/Electronics | √ | ||||
Medical | √ | √ | |||
Optical/Photovoltaics | √ | ||||
Protective/Decorative | √ |